KUBSA: Local artisans of Guledgudda, Karnataka: Ilkal and Khun Indian Textiles
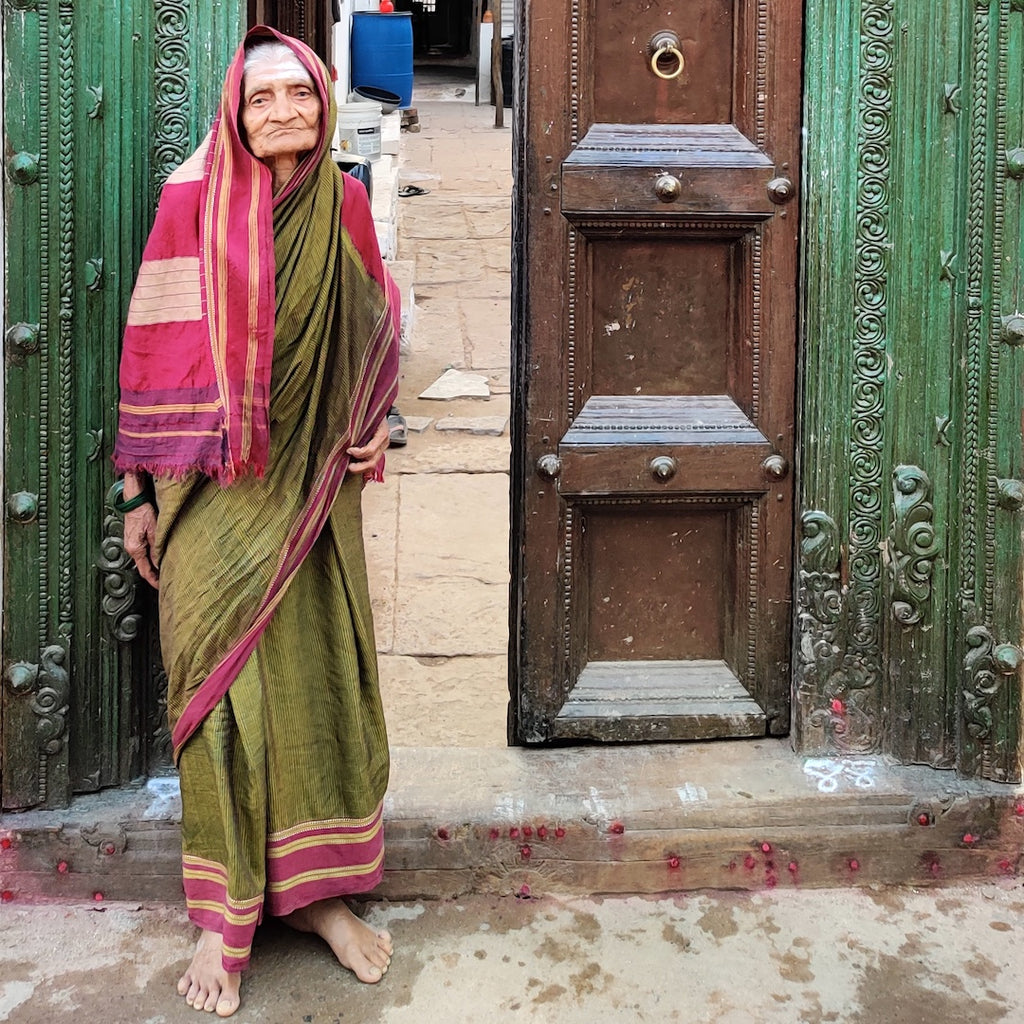
Powered by people, not looms, textile designer Geeta Patil of Kubsa, is transforming traditional Indian textiles, hand woven on the pit looms of Guledgudda.
Power looms outnumber pit looms disproportionately in Guledgudda, Northern Karnataka, today- 4000 power looms to 50-60 hand-looms. Power looms increase production and cut costs wherever possible-replacing local artisans, and the prized Khunsilk with cheaper viscose and polyester.
Instead, Geeta Patil of Kubsa supports local artisans’ livelihoods, from the ground up. Sustainably sourced mulberry silk, cotton and hands-spun khadi once used as a base for Khun, are being revived. While staying true to the original techniques and grammar of traditional motifs, Kubsa's contemporary aesthetic and sustainable design ideologies are shaping new lives for these beloved Indian textiles.
The Guledgudda 'khun' is originally woven for a 'kubsa' or blouse, and paired with the local 'Ilkal' sari, prized by the women of northern Karnataka and southern Maharashtra. It is woven on a 31-inch-wide loom. So precious is the textile, that an entire 'Kubsa' blouse is made of a just a 20-inch-long fabric, sewn optimally to minimize waste. Any shortage is compensated with a gusset!
The familiar Ilkal sari of Karnataka belies the complexity of its making. The Ilkal sari of Karnataka has won a Georgraphical Indicator (GI) tag, for a unique technique called the 'kondi' where the warp of a sari's cotton body is painstakingly interlocked to a silk warp for the 'pallu'. Exclusively done by women artisans, more than 3400 threads are individually looped and joined along the sari width. To complete the sari, two weavers work on the three-shuttle borders in tandem.
The technique was born of necessity. The sari gets its name from the town of Ilkal in Bagalkot district, Karnataka. Set in a cotton growing area, it once had a thriving weavers' community. Until the 1900s it was the highest tax-paying district in the region. Merchants introduced silk in the 18th century, but as it was expensive, it was used only for the 'pallu'. The silk is attached using the 'kondi' technique, and the traditional saree has a red silk pallu with white motifs.

Locally sourced mulberry silk and cotton is natural dyed in indigo, as Kubsa supports the entire ecosystem of artisans’ livelihoods, giving new life to this beloved Indian textile.
Kubsa's checkered Ilkals are a luxurious blend of locally sourced cotton, mulberry silk and hand-spun 'khadi'. The 'pallu' retains the geometric bands, with traditional motifs–the 'latti gunni' or rolling pin, and 'tope teni' or millet.
Often unaccounted is a woman's role in the fibre-to-fabric ecosystem. The weavers, typically men, earns their wage per sari. This overlooks the work of women, unpaid by the master weavers. “At Kubsa, all artisans are considered important and paid fairly. We recognize every woman. We believe in equal pay,” says Geeta Patil.

THE KUBSA COLLECTION
Kubsa's checkered Ilkals are a luxurious blend of locally sourced cotton, mulberry silk and hand-spun. The 'pallu' retains the geometric bands, with traditional motifs – the 'latti gunni' or rolling pin, and 'tope teni' or millet.

“WE BELIEVE IN EQUAL PAY.”
Often unaccounted is a woman's role in the fibre-to-fabric ecosystem. The weaver, typically a man, earns his wage per sari. This overlooks the work of women, unpaid by the master weavers. “At Kubsa, each and very artisan is considered important and paid fairly. We recognize every woman’s skill, dedication and hard work. "We believe in equal pay,” says Geeta Patil.
When you buy a Kubsa sari, a women artisan gets her due too!
Leave a comment